Innovation invariably introduces challenges, both to ways of thinking and to ways of doing. This was particularly true of Frank Whittle’s proposal of turbo-jet propulsion.
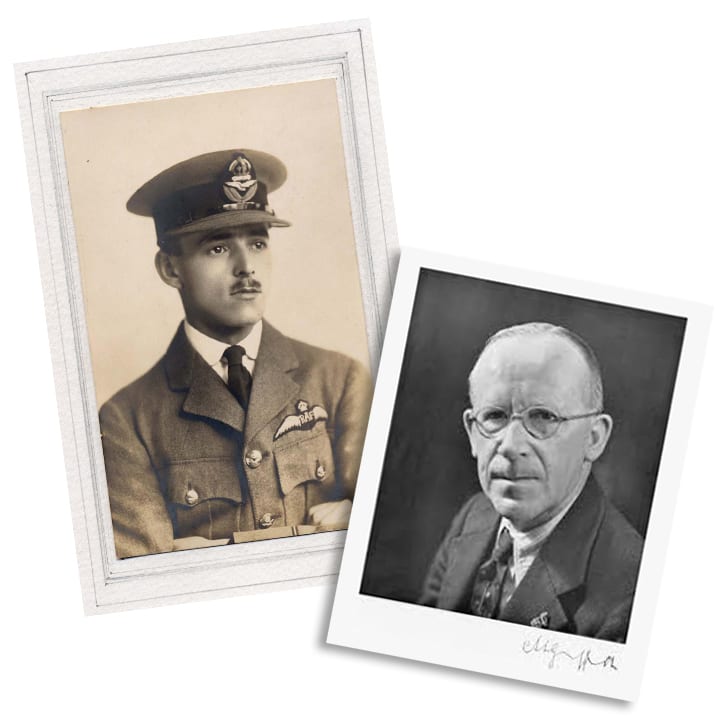
- Pilot Officer Frank Whittle
- Dr A.A.Griffith
His opinion of Whittle’s much simpler turbo-jet scheme was damning. That he found a mistake in Whittle’s calculations could not have helped, although in subsequently revising them Whittle found another error which largely cancelled out the first. Griffiths, however, seems to have underestimated the favourable effect of low intake temperatures at high altitude and of increased compressor efficiency due to ram-effect at high speed – his turbo-prop proposals would have operated lower and slower than Whittle was envisaging. He may also have failed to realised that less oxygen in the thinner air at higher altitudes would be offset by lower drag. The net effect of these factors is that turbo-jet aircraft operate more efficiently at high altitude than at low levels.
- Flight Lieutenant Gerry Sayer
- Gloster E28/39, first prototype

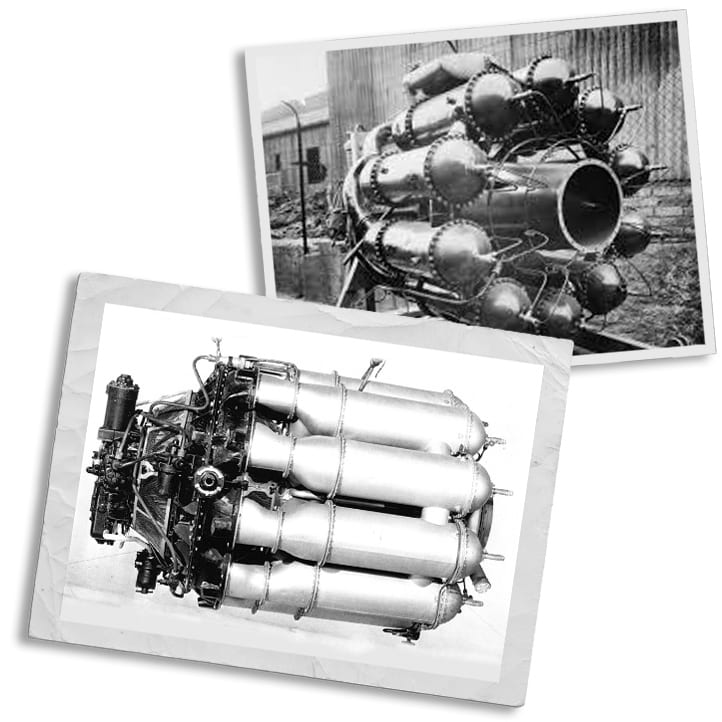
Materials
The subsequent letter to Whittle from the Ministry also stated that gas-turbines were impractical since there were no suitable materials which could withstand the high temperatures and stresses involved, a view which was still substantially true (a matter of chickens and eggs) though based on an earlier (1920) report by the Air Ministry scientist, Dr W J Stern. He, in turn, had based this on the assumption of a bronze turbine rotor and cast iron combustion chamber. In the meantime, the need for high-temperature allows for such applications as internal-combustion-engine exhaust valves was already being tackled.
- W1
- W2B
In practice, the success of W1 did quickly spur research into metals specifically optimised to suit jet engines, with Inco’s Leonard Pfiel being credited with the development of the first of a series of nickel/chrome high-temperature and low creep alloys, Nimonic 80, which was first used in the W.2B. Ironically, this in turn led to the development of a related alloy, Nimonic 80A, specifically for exhaust valves. Soon there were a whole series of other improved nickel-based alloys in the Nimonic family that were and are widely used in later engines and other hostile environments.
Combustion
One of the early combustion test rigs, using a barrel of “white spirit at the BTH facility at Ladywood


Centrifugal or Axial compressor?
Reproduction of drawings illustrating British Patent No. 347,206, filed 16th January 1930
A centrifugal compressor would be simpler and cheaper to produce. It would be more rugged and much more tolerant of the varying intake conditions and rapid throttle changes encountered by a flight-engine. It would however need to run at higher revolutions than an axial. But there was extensive experience of small centrifugal blowers developed as robust aero-engine superchargers. And there was little prior art on axials.
Hans Joachim Pabst von Ohain

In the same time-frame that Ohain was working at Heinkel A.G. (HAG), Dr Herbert Wagner was similarly working on a promising axial form of turbojet at Junkers Flugzeugwerke (JFA). The two projects were secret and unknown to each other. Subsequently, the Wagner project came over to Heinkel and became the He.S30 but was not given support by the German Air Ministry (RLM) who favoured the axial engines then under development at Junkers Motorenwerke and BMW.
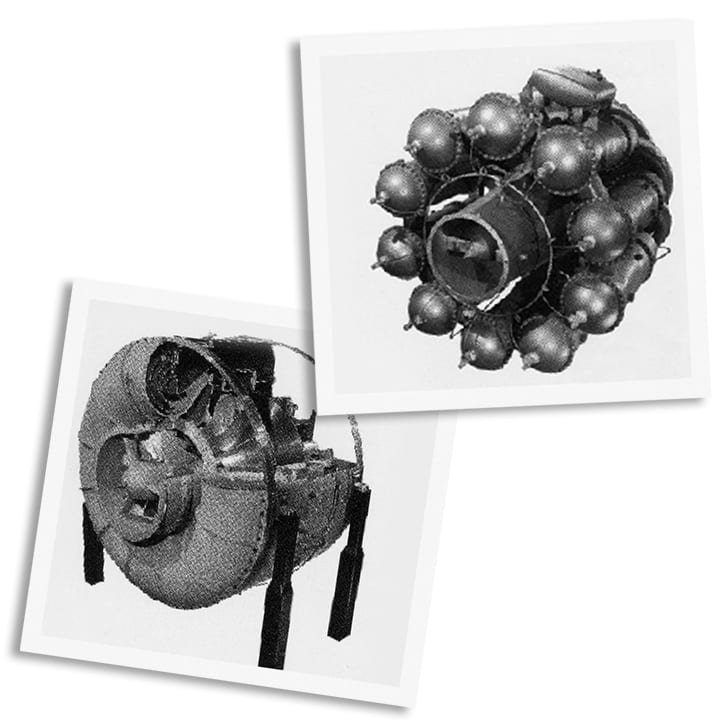
Whittle’s W1 and Ohain’s He.S3B
In Germany, the government had placed contracts in 1937 with 3 engine manufacturers, later including Heinkel who had acquired a large part of a team from Junkers Aircraft, who had not received a contract. The four design teams had each decided to pursue axial compressor solutions – Heinkel now having both an axial and von Ohain’s centrifugal project. These decisions may have been partly influenced by the German Air Ministry (RLM) having carried-out research into axials at the time the British Air Ministry had stopped gas-turbine research. This left only Whittle and von Ohain developing centrifugal engines, although quite unknown to each other.
Manufacture
- Rolls-Royce Derwent
- Rolls-Royce RB41 Nene
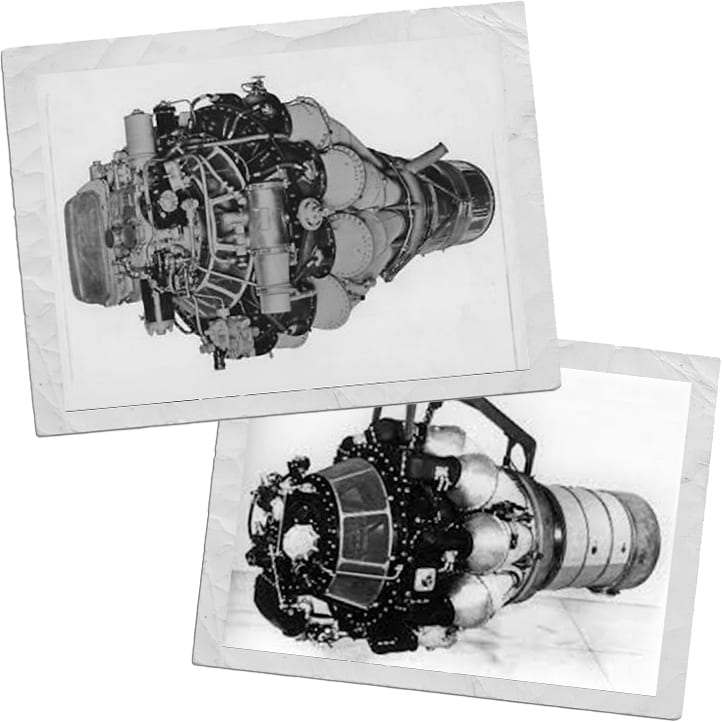
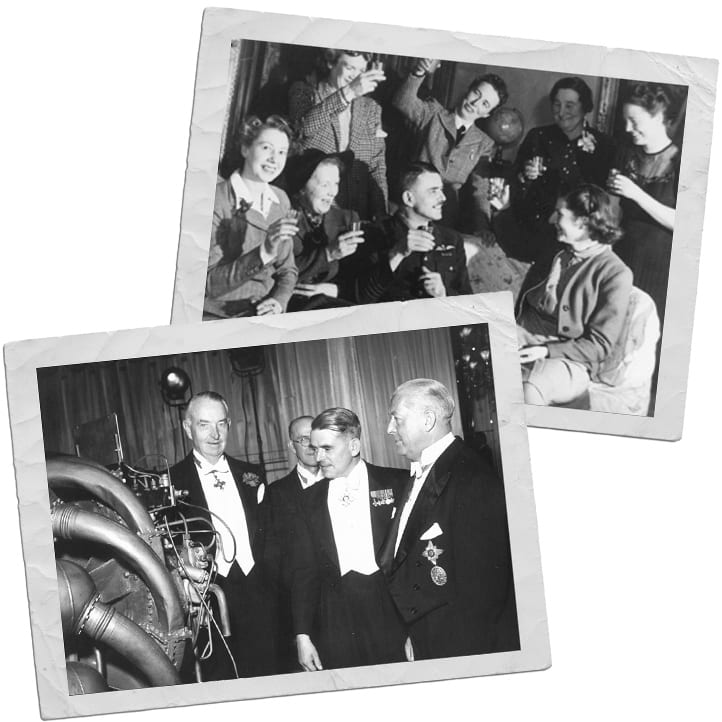
- The wives of the team celebrate success
- Sir Rolf Dudley-Williams, far right, next to his friend Sir Frank Whittle
- In late 1943 Frank Whittle and his team at Power Jets embarked on the design of a high-bypass fan engine based on his ideas formulated c1932 and patented in 1936. This had a nine-stage axial compressor with a final centrifugal stage driven by a two-stage turbine and designated LR1 (Long Range 1). There is no doubt that the axial compressor incorporated the knowledge gained over many years by the RAE, one of whose leading scientists was on loan to the company. Regrettably, the project was cancelled by the government when 50% complete and it would be a further 10 years before the first production low-bypass turbo-fan, the Rolls-Royce Conway, would emerge. It would take GE to lead the way into the turbofan era with their TF39 (bypass ratio 8:1) that first ran in 1964.
- Bibliography and further reading.
- Jet – published by DATUM publishing Ltd.
- Turbojet – History and Development by Antony Kay.
- Jet & Turbine Aero Engines by Bill Gunston.
- The Jet Pioneers by Glyn Jones.
- Not much of an Engineer by Stanley Hooker.
- Jet Man by Duncan Campbell-Smith published by Head of Zeus Ltd
- World Encyclopedia of Aero Engines, Bill Gunston, pub. Patrick Stevens.
- http://history.nasa.gov/SP-4306/ch7.htm#132